The concept of mixing
Due to changes in regulations on additives and the complexity of formulations, the components to be mixed in the polyol have very different viscosities, making them difficult to blend or even immiscible.
The result is a foam that is challenging to process, often leading to surfaces in contact with the sheet metal filled with bubbles, adhesion problems, shrinkage issues, and bubbles.
To overcome the miscibility problem of the components, we have developed two elements that allow for the dispersion of additives and gases into very small particles, evenly distributed within the polyol. Consequently, when the polyol is mixed with the isocyanate in the mixing head, the additives become much more reactive, and there is no concentration of random gases or foaming agents that create bubble-filled or “potato field” surface states.
Dispersion is currently an essential element in polyurethane foam production units and yields excellent results for PIR (Polyisocyanurate) foams. It is available in low-pressure form (nucleation air mixture) placed after the dynamic mixer, and high-pressure form (pentane and additive mixture) positioned closest to the mixing head.
Feel free to contact us for further information!
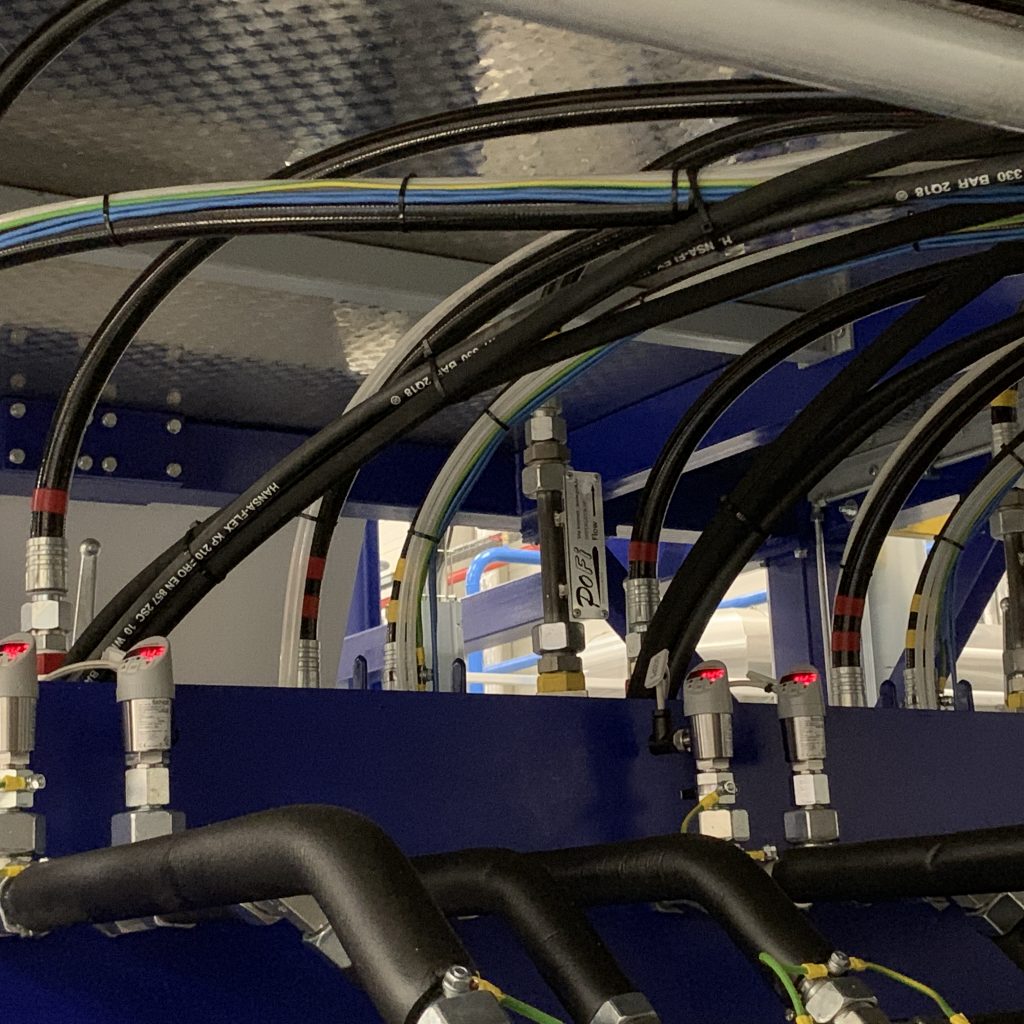
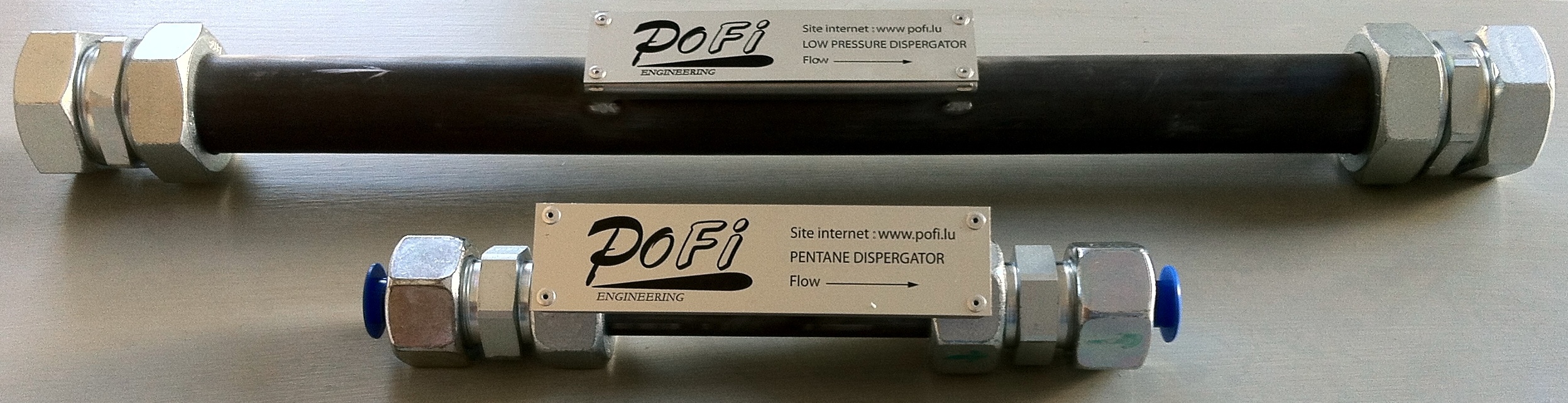